By Jeff Murphy,
April 7, 2020
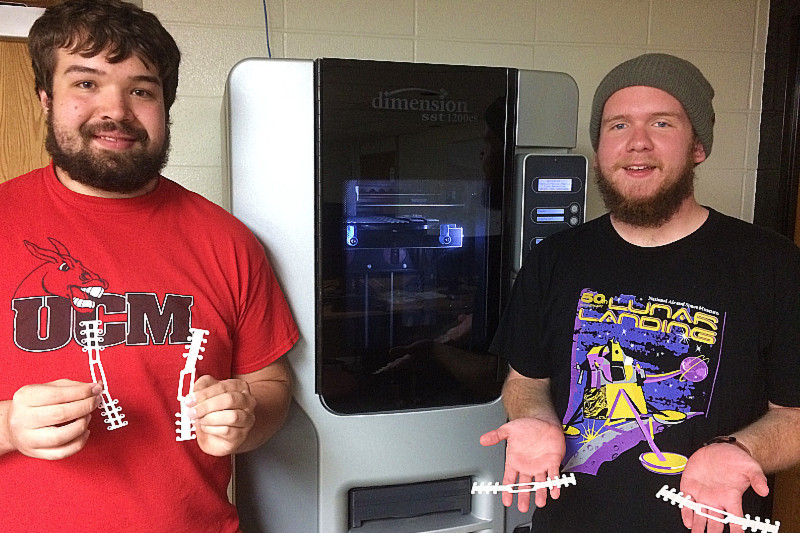
University of Central Missouri students, Matthew Argotsinger, left, Peculiar, Missouri,
and Cameron Rogers, Camdenton, Missouri, display ear guards that were made on a 3D
printer and will help local healthcare workers to be more comfortable wearing protective
gear for long hours. Photo by Paul Brown.
WARRENSBURG, MO – Inspired by action taken by a Canadian youth, two University of
Central Missouri students have found an innovative way to provide relief for individuals
who experience discomfort from extended use of protective masks. The masks are worn
by healthcare professionals on the frontlines of the nation's battle with COVID-19
and are essential for their protection, but the design of these protective items creates
a problem that is recently getting a lot of attention. Many individuals who wear this
protective gear for long periods of time experience pain caused by rubber straps that
dig into the skin behind their ears.
On Monday, April 6, Matthew Argotsinger, Peculiar, Missouri, and Cameron Rogers, Camdenton,
Missouri, began production of a new ear guard they plan to contribute initially to
Western Missouri Medical Center. Through their volunteer efforts, they hope to serve
nearly 600 employees with their new device, 400 of whom are on the frontline serving
patients.
Argotsinger and Rogers are both UCM juniors majoring in Design and Drafting Technology.
They have leadership positions in the American Institute of Building Design (AIBD)
and the Design and Drafting Technology Student Association (DDSA), with Argotsinger
serving as president and Rogers, vice president. Both students have been working closely
with their instructor, Paul Brown, who is currently teaching the Advanced Parametric
Modeling course and 3D Printing.
Dr. Roya Azimzadeh, program coordinator for Design and Drafting Technology, said she
was contacted by Argotsinger, who shared with CADD faculty members his thoughts about
how the program could make a positive contribution to fighting the current pandemic
situation.
“I immediately welcomed the idea and suggested getting started right away,” Azimzadeh
said. Students began working in the CADD Design and Drafting Technology area of the
Grinstead Building, where they have access to three 3D printers which they used to
create a prototype, and continued to produce the first batch of their new device.
Matthew Argotsinger, a University of Central Missouri junior from Peculiar, Missouri,
displays a new ear guard that he and another student created with a 3D printer. It
will eliminate skin discomfort caused by the rubber bands that help hold protective
masks in place. Photo by Paul Brown.
Argotsinger said he got the idea after reading about a Canadian boy, Quinn Callander,
who used a design he found on the internet to create an ear guard that rests on the
back of the head of the individual wearing the mask, and allows the rubber straps
to attach to it, rather than wrap around their ears. His story went viral after his
mother shared it on social media.
“I saw it on Facebook,” Argotsinger said. “He uploaded the design so that anyone could
get access to it and continue on their own. I saw other types of designs, but when
I saw this one, I knew this is something we can work with.”
Argotsinger said one of the issues he and Rogers discovered while working with the
3D printers is that production is a slow process. The students hope to produce up
to 60 ear guards a day to meet local needs as soon as possible. Currently, they are
donating their time and the academic program is covering the cost of the production
materials to make the ear guards possible. For students involved, however, there is
much more in return for their efforts through lessons gained that don’t always happen
in a traditional classroom setting.
“Just reacting fast and appropriately to a situation and using what we have to help
the cause” is a great learning experience, according to Rogers.
Argotsinger echoed that sentiment, adding that “Being able to adapt to a situation
that keeps evolving and then also manipulating a certain design to make it work successfully,
effectively and as efficiently as possible” will help make him better prepared for
the professional world.
Brown agreed, noting, “This is a real-world experience for them using a customer that
has a demand. They are trying to satisfy that demand through increasing production
and productivity. It’s a real good lesson in satisfying a customer.”
While the educational benefits are valuable, all involved are pleased that they are
making a contribution to help those who are on the front line in slowing the spread
of COVID-19 and caring for those who are most affected.